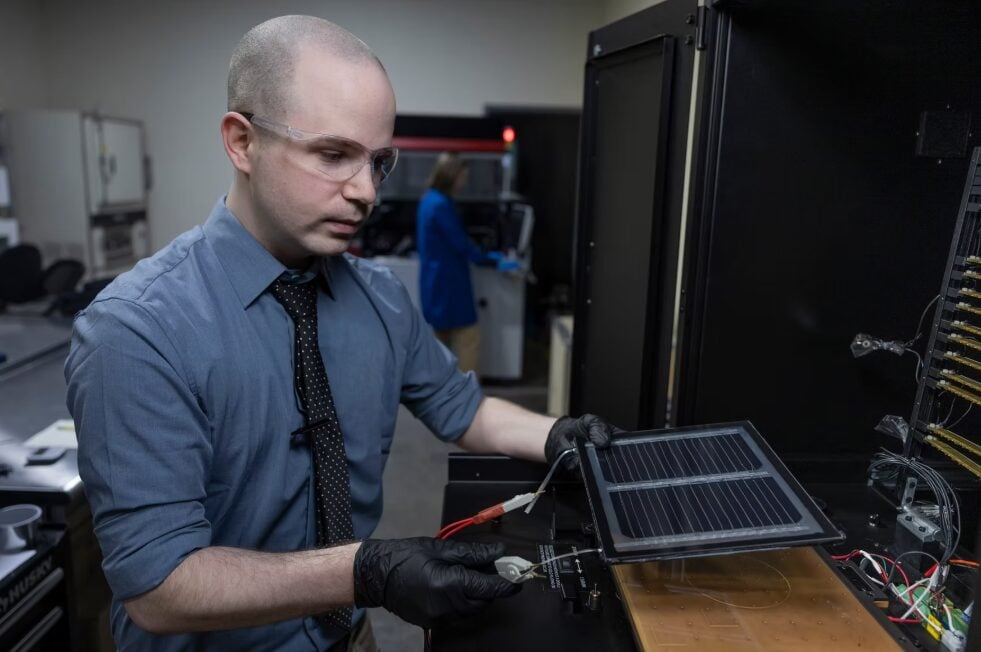
Kentucky-based Bert Thin Films has used a proprietary copper paste on a tunnel oxide passivated contact (TOPCon) M10 solar PV cell with a conversion efficiency of 24%.
The paste, dubbed ‘CuBert,’ aims to replace silver paste typically used in solar cells, in order to cut the cost of producing such cells by reducing reliance on silver, an expensive material. This is particularly significant at present, as the growth of the renewable energy industry has pushed global silver demand to new heights.
Unlock unlimited access for 12 whole months of distinctive global analysis
Photovoltaics International is now included.
- Regular insight and analysis of the industry’s biggest developments
- In-depth interviews with the industry’s leading figures
- Unlimited digital access to the PV Tech Power journal catalogue
- Unlimited digital access to the Photovoltaics International journal catalogue
- Access to more than 1,000 technical papers
- Discounts on Solar Media’s portfolio of events, in-person and virtual
Or continue reading this article for free
This has been driven by the solar industry’s adoption of n-type technology, which requires roughly double the silver per watt of mono PERC (passivated emitter rear contact) technology. This has triggered price rises in the global silver sector, with the International Precious Metals Institute reporting this month that global silver price has doubled since 2019.
Bert Thin Film’s CuBert paste consists of copper, a notably cheaper material. The production of the paste also uses many of the same processes and equipment as the production of silver paste – it can be screen printed, fired in air and processed using the laser enhanced contact optimisation (LEC) process – so Bert Thin Films is hopeful that the replacement of silver paste with its own product will not require significant investment in new machinery and processes.
“This result is more than just a number – it is validation of the core technology that we have been developing,” said Bert Thin Films CEO Thad Druffel. “By enabling high-efficiency cells sustainably and at lower costs, we’re opening the door to more flexible, cost-effective manufacturing pathways for the entire solar industry.”
Alternatives to silver
A number of companies have sought to reduce their reliance on silver consumption in recent years, including Chinese manufacturer Risen Energy, which announced plans to reduce silver consumption for its heterojunction (HJT) cells from 6mg/W to 0.5mg/W. However, simply replacing silver with another material, such as copper, threatens to reduce the conversion efficiency of the cells involved.
In the paper ‘Transition from silver-to copper-based screen printed SHJ solar cells’, published in April, researchers from Fraunhofer and German manufacturer EKRA Automatisierungssysteme found that the “cost-optimised” replacement of silver with copper in solar cells could lead to a “substantial loss” of 0.3-0.4% in conversion efficiency.
However, some results were more encouraging. In a third test, featuring two-thirds less silver than the control variable, the researchers reported that conversion efficiency was “maintained”, while bifaciality was improved by 1%, demonstrating that, at least at the laboratory testing phase, silver can be replaced with copper in the production of cells with no loss of power generation.
Bert Thin Films, meanwhile, announced that it plans to expand its TOPCon products further, looking to work with “pilot-line partners” to scale its copper paste production to commercial volumes, but has not announced a timeline for such developments.
PV Tech publisher Solar Media will be organising the fourth edition of Large Scale Solar USA in Dallas, Texas 29-30 April. After a record year for solar PV additions in the US, the event will dive into the ongoing uncertainties on tariffs, tax credits and trade policies as more domestic manufacturing becomes operational. Other challenges, such as the interconnection queues and permitting, will also be covered in Dallas. More information, including how to attend, can be read here.