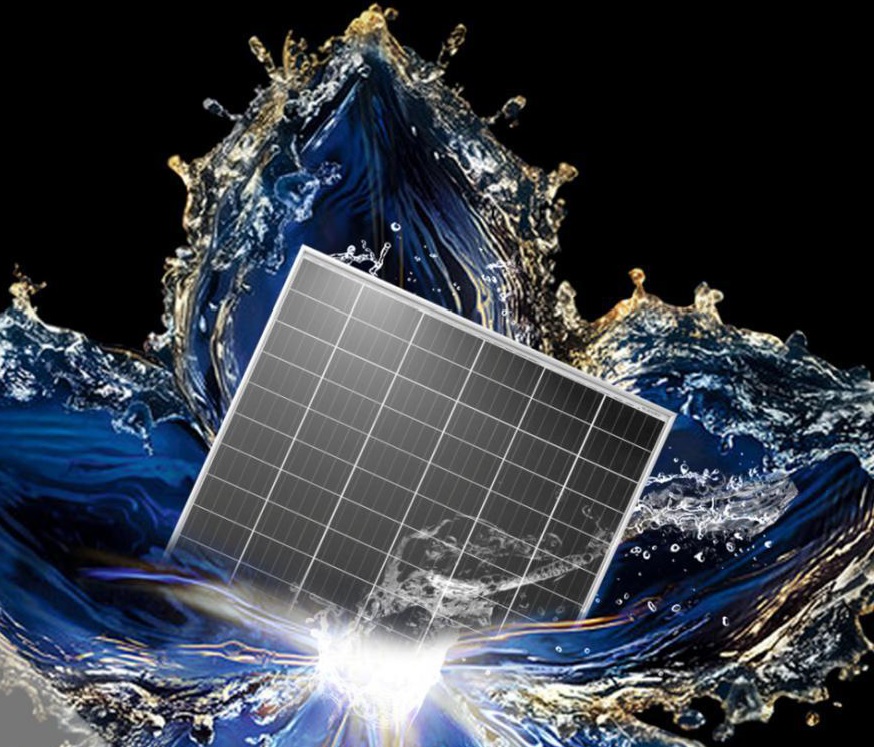
Following the successive release of new high efficiency modules by JinkoSolar, JA Solar, Trina, Risen and others, the debate over wafer size has drawn to a close, at least for the moment. PV modules have too entered a new era featuring “big” products topping 500MW.
JinkoSolar’s new Tiger Pro currently occupies the top spot in the PV industry’s efficiency ranking lists. Its highest output can reach up to 580W, which is 40% higher than that of other mainstream modules in use at large-scale power plants. This number also signifies an historical peak in module efficiency.
Unlock unlimited access for 12 whole months of distinctive global analysis
Photovoltaics International is now included.
- Regular insight and analysis of the industry’s biggest developments
- In-depth interviews with the industry’s leading figures
- Unlimited digital access to the PV Tech Power journal catalogue
- Unlimited digital access to the Photovoltaics International journal catalogue
- Access to more than 1,000 technical papers
- Discounts on Solar Media’s portfolio of events, in-person and virtual
Or continue reading this article for free
JinkoSolar is one of the companies leading the industry today and it believes that the next big problem is power density, and a change in size is not the only way of achieving an improvement in this area. Wafer size, according to JinkoSolar, should not be mistaken as a technical specification or even a bidding criterion.
Wafer size does not matter
Dany Qian, vice president at JinkoSolar, told PV Tech that internally, the company had reflected as to whether it had in fact misguided the industry by mentioning the 158mm wafer size of its Cheetah series of panels.
“Everyone is overly concerned about wafer size, which means little to the customer. The more power they get from one panel, the better return of investment is expected. In other words, module efficiency and power density are meaningful metrics for judging how powerful a particular panel is.
“Take pizza for example, it's not that a 12″ pizza is necessarily better than an 8″ one, it's more about how good the pizza tastes. For modules, the only thing that matters is technology. Technology is the driving engine for leading massive improvement,” Ms. Qian said.
Having recently interviewed a number of module manufacturers, PV Tech has found that it is not only the top companies that feel somewhat frustrated at the ongoing debate over wafer size, other manufacturers sharing the same feelings. Indeed, constant size enlargement is facing growing opposition.
Ms Qian continued, “It's all about the mindset. Why do you think it is reasonable to categorise products into 166mm, 210mm and 180mm? It does not give you any clue or indication what power and performance they refer to, and what your project’s engineering design will be based on. For instance, with JinkoSolar’s optimised tiling ribbon and multi busbar process used with the Tiger Pro, this marks a chance to jump past the counterparts using bigger wafers, of 210” in size, in generation performance. So the race for output and power density, rather than wafer size, will bring some healthy competition to the industry and make model selection easier for project design.”
It’s important to note that power performance doesn’t scale exactly with wafer size. The way each wafer provider measures can vary from one to another, so it’s best to take them more as marketing terms used to segment products rather than exact measurements of power or efficiency. For example, JinkoSolar’s 580Wp Tiger Pro is expected to compete with Trina and Sunrise’s 210” products.
“In addition, we might reach a limit point at which we can no longer continue to make bigger, but we still need more powerful, more efficient panels. So more focus on technology and process improvement is our approach to continue growth,” Ms.Qian continued.
Return to technology and cost reduction
Module output has reached 500W and will continue to go upwards, especially amid the decline of global PV subsidies and PPAs. ‘500W-plus’ or even 600W modules will be quickly popularised in the new decade when all companies will be working towards LCOE reduction.
Only last month, Abu Dhabi quoted the world's lowest tariff at $0.0137/kWh, or 1.37 cents/kWh, which is equivalent to less than RMB 0.10/kWh, for a 25-year long-term PPA.
“Prices as low as 1.37 cents are coming out, and for the power plant investors, bidding costs are falling so fast that what they really need is a high efficiency product.
“Now that we are heading towards parity and the global LCOE is falling quickly, the industry is facing greater price pressure as a result. If a module plant can deliver more efficient products that are capable of accommodating downstream designs, then the cost pressure can be quickly mitigated.”
Chaojie Zhou, JinkoSolar's global director of product management, explained that module output should continue to be increased, but such increases cannot always be achieved by size enlargement. LCOE can be reduced by means of high energy density; this is one principle guiding JinkoSolar’s product design and it is also the reason why the company has underscored the need to maximize the use of surface area.
In the future, JinkoSolar will focus on innovation and technology upgrades. There is still room for improvement in p-type cell efficiency, for example, and PERC mono cells. Another future direction for cell R&D is the integration of high-efficiency cell technologies, with module process optimization a key factor that has allowed JinkoSolar to succeed in such a competitive market.
JinkoSolar's Tiger Pro uses multi-busbar and tiling ribbon technology to achieve a conversion efficiency of 21.6%. In addition to its power generation performance and excellent temperature coefficient, Tiger Pro, by virtue of its high energy density, also presents a lower degradation rate (2% in the first year) and better open-circuit voltage. The LCOE has been significantly reduced to maximise the generation capacity of a power plant.
“JinkoSolar is a module manufacturer, but we have always developed our products with a customer and market-oriented mindset. Economic benefits of a project, construction design, operation and maintenance and intelligent manufacturing are all key considerations for us.
From the customer perspective, when it comes to a new product, the first priority is technology, and the second is whether your capacity can meet his needs and match his projects. JinkoSolar has a supply chain covering wafer, cell and module and we are capable of supplying at least 10GW of these products,” added Zhou.
The Tiger Pro module is expected to enter mass production in Q3 2020, with a planned capacity of 10GW. Shipments are expected to start in Q4 2020 with ramped production expected in 2021.