Introduction
In 2024, the market share for n-type cell technology surpassed that for p-type cells for the first time, with p-PERC cells quickly exiting the stage. N-TOPCon cells have emerged as the mainstream technology, with HJT, IBC and perovskite-silicon tandem cell technologies forming a diversified competitive landscape of passivated contact cell technologies.
TOPCon: Rapid technology development and new boosts for improved module reliability
The PV industry has always embraced technological innovations, striving for higher conversion efficiencies and lower levelized cost of electricity (LCOE). Since the mass production of TOPCon cells in 2022, their high performance and low cost have allowed them to rapidly capture the market from their p-type counterparts. In just two years, the test efficiency of production n-TOPCon solar cells has risen significantly from 24.5% to 26.5%. Compared to traditional PERC cells, the efficiency gains for n-TOPCon cells come mainly from improvements in open-circuit voltage (Voc), which result from the excellent passivation effect of the rear-side tunnel oxide/n-poly layer, as well as the passivation provided by the AlOx/SiNx layer on the p+ emitter on the front side.
The early generation of production TOPCon cells used silver-aluminium paste for front-side metallization. The aluminium in the paste promotes the formation of silver-aluminium spikes during firing which provides ohmic contact and effectively solves the contact challenge with the p+ emitter. However, the paste components required to form these spikes inevitably cause significant damage to the front-side AlOx/SiNx passivation layer, introducing excess metallization induced recombination loss. This critical recombination issue leads to significant Voc and efficiency losses, greatly limiting the continued efficiency improvement of TOPCon cells.
In 2023, Laser Enhanced Contact Optimization (LECO) technology achieved large-scale production for TOPCon cells and quickly became an industry standard. This technology, combined with specialized metallization paste design enables: (1) controlled local openings in the AlOx/SiNx passivation layer during the firing process, minimizing damage to the p+ side passivation to improve Voc. At this stage, the cell is still semi-finished wherein the electrical contact between the metal grid and the silicon is extremely poor; (2) after firing, the cell is scanned with a laser while under reverse bias, causing high-density currents to flow through the high resistance contact points. The instantaneous local high temperature from resistive heating of the high current density alters the physical structure of the poor contact points (as shown in Figure 1), forming ohmic contact points at the tips of the pyramids that are significantly smaller than traditional silver-aluminium spikes, thereby greatly reducing the contact resistance between the silver grid and the silicon.
LECO technology addresses the major challenge of balancing metallization induced recombination loss and ohmic contact difficulties in the front-side metallization of n-TOPCon cells. It simultaneously makes significant improvements to both the Voc and fill factor (FF) of n-TOPCon cells, resulting in an efficiency gain of 0.3% to 0.6%. Furthermore, LECO opens up opportunities for further optimization of the boron emitter toward ultra-high sheet resistance diffusion process for n-TOPCon cells.
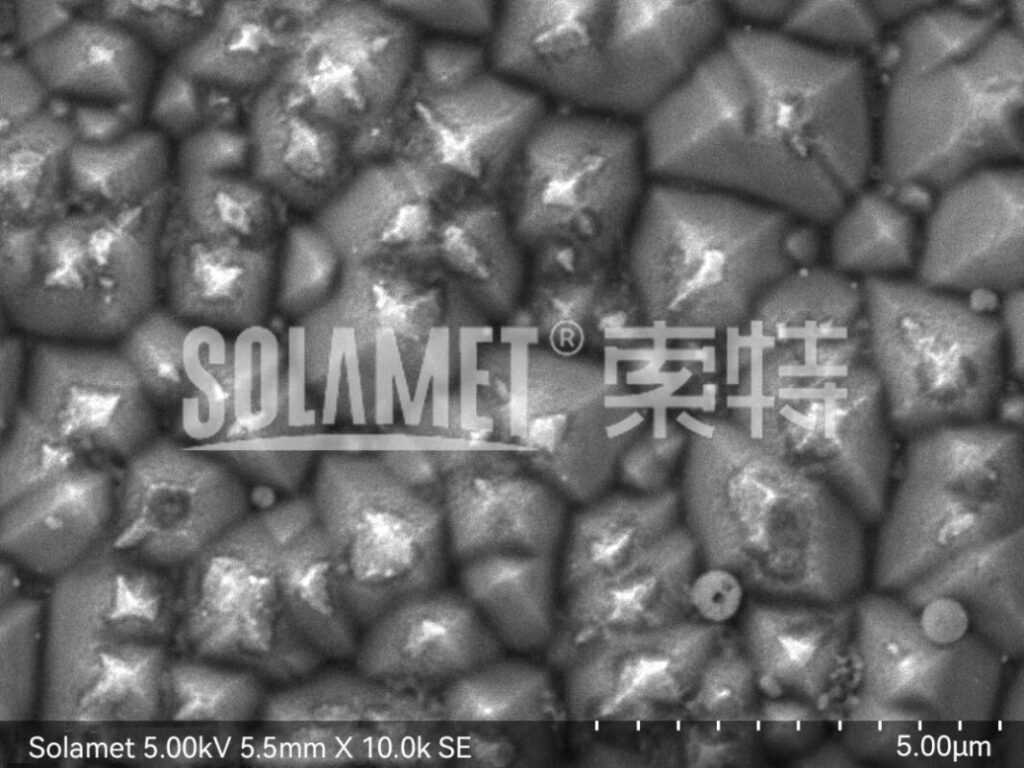
It is worth noting that conventional silver-aluminium paste provides little additional efficiency gain when used with LECO technology, further demonstrating the importance of the specialized LECO metallization paste in controlling the selective etching of the AlOx/SiNx passivation layer, as well as the number and size of initial pre-contact points formed during firing. Solamet, with its extensive R&D expertise and close collaboration with equipment and cell manufacturers, in 2023 became the first global supplier to achieve mass production of LECO-specific pastes, the PV3NL series of metallization products, contributing significantly to the widespread adoption of this technology.
Another major challenge for the n-TOPCon cell is its high silver consumption. Unlike the p-type PERC cell, which uses aluminium paste on the rear side, the n-TOPCon cell requires silver paste on both the front and rear sides, including both the busbars and finger lines. Using screen design with thinner mesh and emulsion as well as finer finger openings has become the main approach to reduce silver consumption in n-TOPCon cells. The aluminum-free LECO-specific paste significantly improves gridline resistance, and LECO technology has also greatly enhanced silver-silicon ohmic contact, both of which pave the road for fine-line screen printing for n-TOPCon. As manufacturers successfully apply the learnings and experiences of fine-line screen-printing techniques used in PERC cells to TOPCon cells, the silver paste consumption for 182mm TOPCon cells has reduced from over 140mg per cell in the early stages of mass production to about 80mg per cell, a reduction of more than 40%! Furthermore, Solamet introduced the PV6NL series of low solid-content (89%) rear silver paste for TOPCon cells, which can reduce rear side silver consumption by 5-10% per cell while increasing cell efficiency by 0.03-0.05%, further driving progress in cost reduction and efficiency improvement.
According to a module reliability evaluation report released by PVEL in June, among the 53 global PV companies that participated in testing, 85% of double-glass n-TOPCon modules passed the DH2000 test, while only 46% of single-glass n-TOPCon modules were successful. The report revealed that early TOPCon technology still has shortcomings in terms of resistance to damp-heat aging. Wu et al., in an article titled “Enhancing the Reliability of TOPCon Technology by Laser-Enhanced Contact Firing”, demonstrated that the use of aluminium-free silver paste in LECO technology significantly improves the degradation performance of modules under DH1000 testing. Since such testing generally takes a long time, cell manufacturers typically use acetic acid corrosion tests as an accelerated simulation. Applying acetic acid vapour or solution to cells in a sealed environment at a preset temperature for several hours has gradually become an important evaluation method for cells aimed at single-glass modules. However, the different acetic acid corrosion testing methods and standards used by manufacturers lacks consistency. While the correlation between acetic acid corrosion test results and actual reliability of modules requires further verification and mechanistic understanding, metallization pastes have continuously progressed to improve the reliability of cells and modules without sacrificing efficiency.
HJT: Now is the time for efficiency improvement and cost reduction
The heterojunction (HJT) structure was first proposed by scientists in the 1970s, and HJT technology has undergone more than 50 years of development. LONGi has pushed the world record for the conversion efficiency of laboratory HJT cells to 26.8%. As a disruptive low-temperature passivated contact cell technology, HJT has attracted considerable interest from investors due to its high efficiency, simpler process, potential for thinner wafers, strong resistance to light-induced degradation (LID) and high bifaciality. However, challenges such as high capital equipment investment costs and high silver paste consumption have limited the industrial scale adoption of HJT compared to mainstream n-TOPCon cell technology.
Traditional high-temperature cells typically undergo metallization at 700-800°C to achieve silver-silicon ohmic contact. In contrast, the metallization process for HJT cells only allows for low-temperature processes below 200°C in order to protect the cell’s thin-film structure from damage. In industrial mass production, HJT cells most commonly use screen printing and low-temperature curing metallization pastes. This poses high demands on the bonding strength and contact resistance between the metal electrodes and the transparent conductive oxide (TCO) layer, as well as the grid resistance of the metal electrodes themselves. At the same time, to further improve the cost structure to enhance the competitiveness of HJT technology, cell manufacturers have been aggressively promoting the development and application of silver-coated copper pastes to reduce metallization costs. However, the introduction of silver-coated copper pastes leads to higher grid resistance, and ensuring the reliability of cells and modules while preventing copper oxidation remains a key concern for raw material, paste, and cell module manufacturers.
IBC: Riding on the momentum of passivated contact
The IBC (interdigitated back contact) cell structure has always been a representative of high-efficiency solar cells. Its leading efficiency is attributed to the interdigitated arrangement of metal electrodes on the rear side of the cell, while the front side remains free of grid shading, providing high light absorption and an aesthetically pleasing design. As silicon wafers and cell technologies transition from p-PERC to n-TOPCon, IBC cells are also evolving rapidly to pursue higher efficiency and competitiveness. The traditional p-IBC is gradually becoming obsolete, and future IBC development will focus on the fully passivated contact concepts of n-TOPCon back contact (n-TBC) and heterojunction back contact (HBC). The competition between TBC and HBC is essentially a further clash between TOPCon and HJT technologies within the IBC cell structure.
The development of IBC technology has been limited by its relatively low bifaciality, complex manufacturing processes and high technical barriers, which restrict its application scenarios. Currently, leading companies like LONGi and Aiko are firmly committed to developing n-TBC technology, while HBC technology is still in the R&D stage, with its industrialization progress lagging behind that of n-TBC.
From the metallization solution perspective, the paste requirements for HBC are quite similar to those for HJT, while n-TBC requires significantly different pastes compared to n-TOPCon. Since the grid lines of IBC cells are located on the rear side, the demand for precision line width control is reduced. Historically, due to differences in paste systems, the line width control ability of HJT pastes has been much worse than that of n-TOPCon front-side pastes. The reduced demand for precision line with control in IBC cells presents a significant advantage for HBC.
One of the major challenges in n-TBC cell manufacturing is the difficulty in contacting the p-poly region. Due to the lack of free electrons in the p-poly region, it is difficult to form ohmic contact points (i.e. silver microcrystals) during the firing process as the reduction of Ag+ ions within the glass is inhibited. In n-TOPCon cells, this issue is solved by using LECO technology or silver-aluminium paste. However, due to the low built-in potential of IBC cell structure with the n and p regions interdigitated on the rear side with very small spacing, applying LECO would lead to current leakage. Additionally, in the metallization region, the presence of the p-poly layer makes it impossible to use silver-aluminium paste to improve contact. Therefore, the contact challenge for the p-poly region cannot be resolved by simply adapting existing n-TOPCon front-side metallization solutions. This presents a significant challenge, requiring the development of unique inorganic systems to balance metallization induced recombination and achieve ohmic contact at the same time. Moreover, because the n-poly and p-poly regions are co-fired at the same temperature, the firing window compatibility of metallization pastes in both regions imposes even higher requirements.
Perovskite-Silicon Tandem: Leading the pack, yet facing significant challenges
The theoretical conversion efficiency of single junction silicon cells is 29.4%, while the theoretical efficiency limit of perovskite-silicon tandem cells can reach around 43%. Many types of silicon-based cells can be used as the bottom cell for perovskite tandem cells, including PERC, TOPCon, HJT, and IBC. In 2024, LONGi pushed the efficiency record for M6-sized perovskite-silicon tandem cells to 30.1%. The company also holds the world record for lab-scale tandem cells at 34.6%, showcasing unparalleled potential in conversion efficiency.
However, despite the significant potential in cell efficiency, the commercialization of perovskite or perovskite-silicon tandem cells faces numerous challenges, including material system stability, large-area growth of perovskite thin film layers, and tandem structure design and implementation. Among these, metallization remains a key bottleneck for large-scale mass production of perovskite-silicon tandem cells. Considering the specific characteristics of perovskite materials, electroplating metallization is challenging to apply to perovskite-silicon tandem cells. Therefore, breakthroughs in conductive paste metallization technology is needed to usher the PV industry into the perovskite era.
Since the launch of the world’s first commercial low-temperature conductive paste for CIGS thin-film cells in 2009, Solamet has continuously invested in R&D in developing novel low-temperature pastes. From 2021 to 2023, Solamet developed PV43B – thermoplastic ultra-low-temperature curing silver paste, and PV43C-thermosetting ultra-low-temperature curing silver paste specifically designed for perovskite-silicon tandem cell application. Both of these ultra-low-temperature curing pastes have been highly recognized by global customers for their excellent bulk conductivity and contact performance. At present, Solamet® PV43B and PV43C have become standard pastes for the development of perovskite tandem cells by many customers worldwide.
Applying traditional HJT low-temperature pastes (with a curing temperature around 200°C) to perovskite tandem cells, which require a much lower curing temperature (around 130°C), results in a dramatic increase in bulk resistivity (4-5 times higher) and a corresponding rise in contact resistance. These lead to a significant drop in the fill factor. In contrast, Solamet PV43B and PV43C silver pastes maintain excellent bulk resistivity (5-8 µΩ·cm), even when cured at temperatures below 130°C (as shown in Figure 2). Moreover, PV43B and PV43C each have distinct characteristics that allow customers to choose based on their specific needs, among which is the curing temperature window as shown in Figure 3. PV43B offers an exceptional curing temperature window, as low as 90-100°C, while PV43C provides better aspect ratios for fine-line printing. Thus, customers can select the appropriate paste based on their curing temperature requirements, line geometry, and line resistance needs (as shown in Figure 4). Solamet’s diverse and differentiated product portfolio can help each customer to adapt and evaluate their evolving technological needs in R&D, pilot and mass production, accelerating the development of perovskite tandem cell technology.
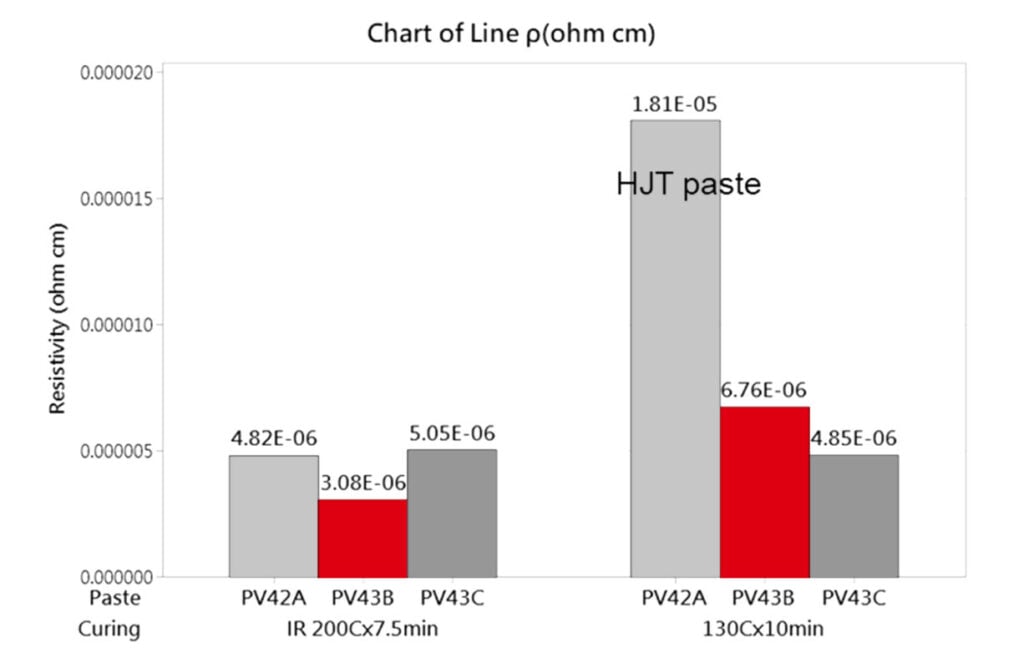
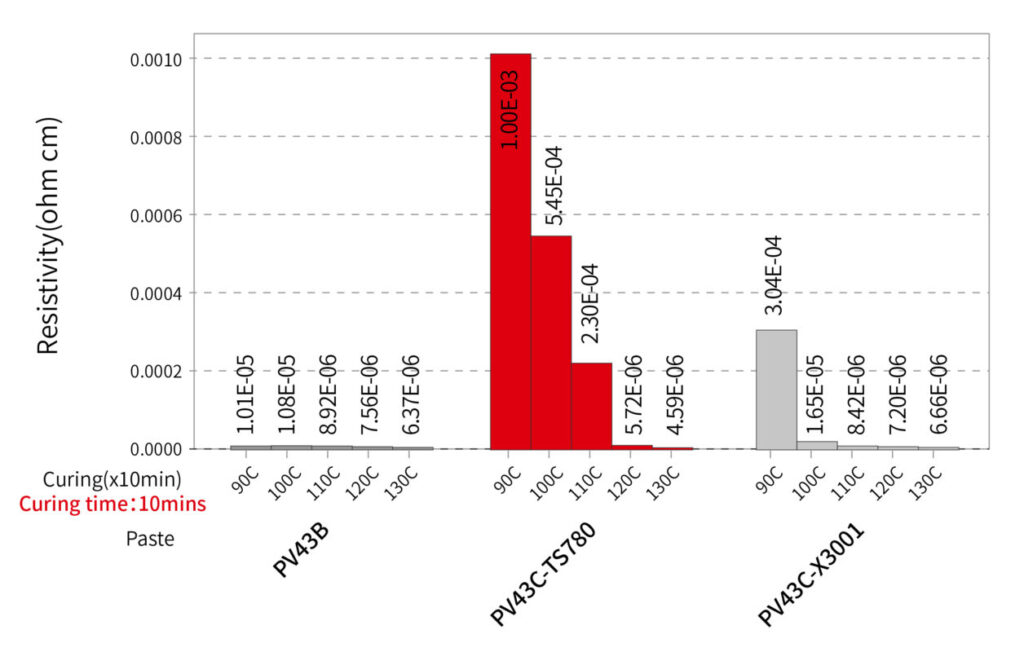
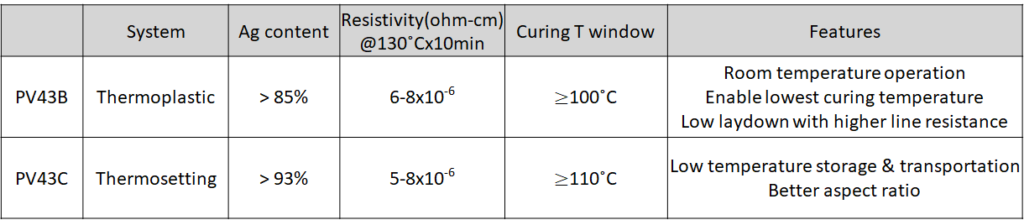
Conclusion
With n-TOPCon cell as the current mainstream technology, a competitive landscape of various high-efficiency passivated contact cell technologies has emerged. The development of new cell technologies also brings new metallization challenges. Reflecting back, since the introduction of the world’s first conductive paste for PV applications in 1983, Solamet has played a crucial role in nearly every technological upgrade in the industry, from p-BSF, p-PERC and CIGS, to n-PERT/TOPCon and IBC cells. Today, Solamet continues to lead the PV metallization paste industry with its specialized R&D capabilities, comprehensive intellectual property system, diverse product portfolio and exceptional global customer service and will continue to push the boundaries of technology, turning high-efficiency cells from possibility into reality.