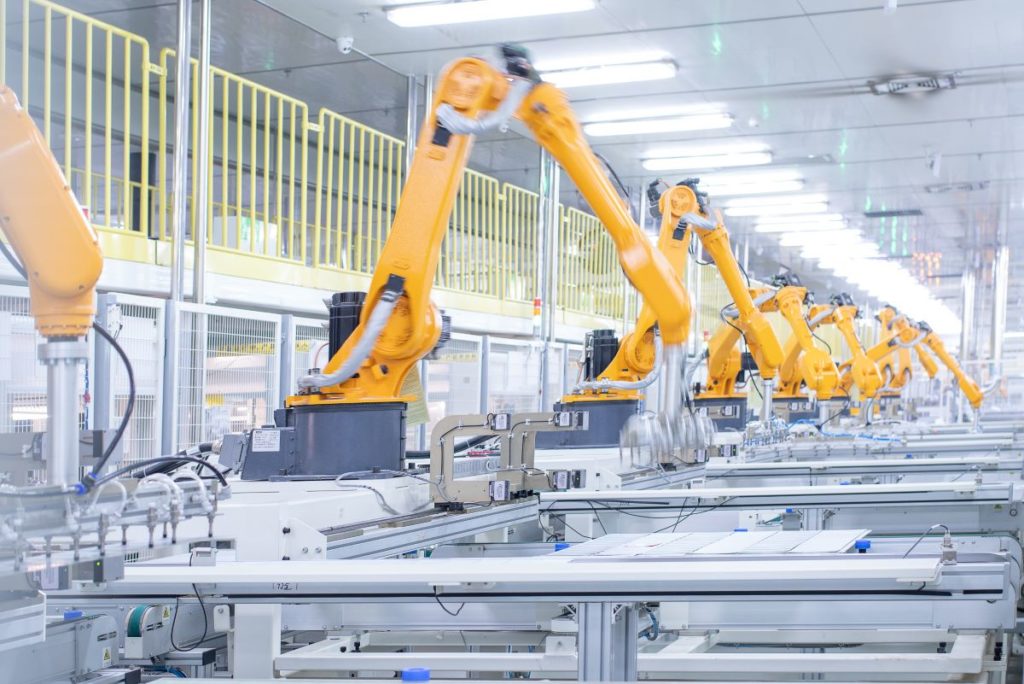
For the past two years, JinkoSolar has invested in increasing its module capacity for which it expects to reach 110GW of annual nameplate by early 2024. This increase was primarily due to the company’s shift from p-type to n-type capacity, and with the selection of tunnel oxide passivated contact (TOPCon) as the new technology for its products.
PV Tech spoke with Jinko’s Victor Wei and Wally Zang, Senior IR Director and Technical Service Centre General Manager respectively, about the company’s investment in TOPCon, its fully vertically integrated plant currently being built in China’s Shanxi province and how it is looking at module products for deployment in offshore solar projects and subject to hail conditions.
Unlock unlimited access for 12 whole months of distinctive global analysis
Photovoltaics International is now included.
- Regular insight and analysis of the industry’s biggest developments
- In-depth interviews with the industry’s leading figures
- Unlimited digital access to the PV Tech Power journal catalogue
- Unlimited digital access to the Photovoltaics International journal catalogue
- Access to more than 1,000 technical papers
- Discounts on Solar Media’s portfolio of events, in-person and virtual
Or continue reading this article for free
Investing capex in n-type technology
In an editorial blog for PV Tech in September, Finlay Colville, head of research at PV Tech, wrote an article about JinkoSolar getting on track to regain the first position for module suppliers in 2023 and how the company had invested capital expenditure (capex) through the value chain, which it already did in 2016 when it reached the top position for several years.
But between 2019 and 2021 the company had its finances restrained as it was only listed in overseas markets.
“We kind of held back for two years and prepared for the next wave of technology. It is only after we went public on the A-share stock market that we tried to make up for our losses from the last two years,” explains Wei.
During these two years the company’s integration rate – between cell and module annual nameplate capacity – also grew from nearly half to above 80%, adds Wei.
From ingots to modules, under one roof
A clear example of this increased integration is the construction of a fully vertically integrated plant, in the Shanxi province, that would go from ingot to modules in the same location and is expected to have an annual nameplate capacity of 56GW, of which the 1st phase of 14GW is expected to be operational by the end of the first quarter of 2024.
Even though a plant of this magnitude requires an area big enough to have everything in the same location, it will also bring advantages in terms of cost. The need to pack, unpack, transport and even store each process of making the modules is therefore lifted and eliminates these extra costs that were non-deniable with having plants in several locations.
“There’s another advantage, which is at the automation level,” says Zang, adding: ”We can design the automation line directly from the wafer factory to the cell factory. It’s very convenient for us to improve our automation level.”
Having control of the entire production line with each section next to the other it will be much easier to get feedback from the entire production line when new technologies are introduced, adds Wei. “It can be really helpful in terms of traceability, which is a key factor for us to export to the US market or for future new markets.”
The third advantage of a fully vertically integrated plant, is in the supply chain, explains Zang. Given that it is very centralised it makes it much easier for the upper and lower limit suppliers to build capacity near the Shanxi plant.
“This production model is now only in the Shanxi province, because the model itself can be quite challenging. We will spend some time to see how well we can handle that,” says Wei. For the time being, Shanxi will be the company’s main focus for its capacity expansion over the next two years.
Customised module products for hail and offshore solar
If the company still has room to improve its cell efficiency, it is also working on improving its module products, says Zang. The company has been looking into two specific areas with ever-increasing demand: hail and offshore solar.
Interest in extreme weather continues to be high – and was recently the cover issue of our latest journal, PV Tech Power 37– especially in the US and has been a focus from tracker providers releasing products targeted to that issue. High hail resistance in modules has been an increased demand from JinkoSolar’s customers, says Zang and the company is looking to customise its products in order to hit the requirements demanded from hail.
Even though still a niche market for the deployment of specific modules, JinkoSolar has been working towards adapting its modules for offshore solar, a market that is expected to grow in the coming years, and for which the Chinese government aims to reach an installed capacity of 20GW from offshore solar alone in the coming years.
Interest in floating solar (FPV) and offshore solar is poised to grow in the coming decade and will mostly be led by China and countries in Southeast Asia such as Indonesia, Vietnam and Thailand due to a lack of available land.
“We’ve run a field test program with some of our partners on seawater, one year ago,” says Zang about the company’s progress in making modules for offshore sea, and added that thanks to these testing, the company also secured a 1GW module supply for offshore projects.
Seawater will require a better reliability performance from modules to be used in harsher environments adds Zang, which will need to have a special design and more protection against seawater corrosion to be used in offshore PV projects.
“BC is a platform technology”
Regarding other technologies that could compete with TOPCon, JinkoSolar sees TOPCon’s lead still far ahead of the competition with only heterojunction capable of getting head to toe, but heterojunction’s equipment cost still remains higher. “Leading is not only about product performance itself, it’s also about the cost,” says Zang.
“TOPCon is still leading in terms of cost effectiveness, especially compared with HJT technology, because of its low temperature process that requires low temperature silver paste, which is dramatically more expensive than the paste we are using in TOPCon cell structures,” adds Zang.
When asked about Professor Martin Green’s comment that interdigitating back contact (IBC) technology would end up being the leading technology in the long run, Zang sees it more as a platform technology that can be combined with other existing technologies such as TOPCon or passivated emitter and rear cell (PERC).
“I don’t think BC technology itself is in a very competitive or alternative position with TOPCon, or even PERC.”
On top of that, BC still needs to resolve some of its challenges which includes costs that are even higher than HJT, yield and complexities of its back structure as well as the patent issues which are “very well protected”, says Zang.
In order for a technology to become mainstream and/or replace another one, as TOPCon is currently doing with PERC, it needs to have a similar cost or even lower, adds Wei. The other important aspect is that cell efficiency needs to be higher than the previous technology at least one to two percentage points higher.
“They [other technologies] either have a much higher cost, or just similar or even lower efficiency rate or power output. For BC, due to its changing structure, it can enhance the efficiency rate for 0.3 to 0.5 percentage points, but that is not enough to distinguish it from TOPCon cell,” explains Wei.
Moreover, with TOPCon being the main technology for the majority of the industry, this in itself fuels the competitiveness of the technology. “ With all the other players following in the path of TOPCon, it can help TOPCon be more competitive. The more technology, the more capital and the more players are in this field, it can help the ecosystem and the efficiency rate go higher and its costs go lower.”