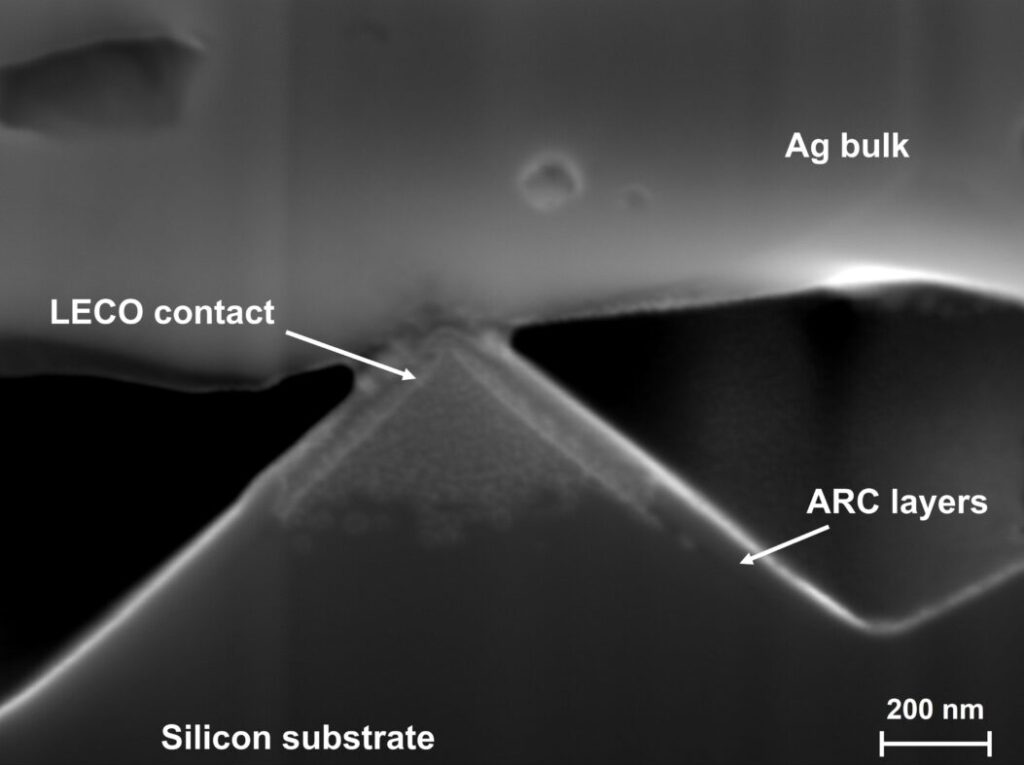
Laser-assisted firing is a major breakthrough in solar cell technology because it can solve one of the key issues causing poor reliability in tunnel oxide passivated contact (TOPCon) solar cells, according to a scientist from Australia’s University of New South Wales (UNSW).
Bram Hoex, deputy head of the School of Photovoltaic and Renewable Energy at UNSW, tells PV Tech Premium that laser-assisted firing is “the biggest innovation in solar cell manufacturing in the last couple of years”.
Unlock unlimited access for 12 whole months of distinctive global analysis
Photovoltaics International is now included.
- Regular insight and analysis of the industry’s biggest developments
- In-depth interviews with the industry’s leading figures
- Unlimited digital access to the PV Tech Power journal catalogue
- Unlimited digital access to the Photovoltaics International journal catalogue
- Access to more than 1,000 technical papers
- Discounts on Solar Media’s portfolio of events, in-person and virtual
Or continue reading this article for free
Hoex and colleagues from UNSW and Chinese module manufacturer Jolywood wrote in a July paper that: “Laser-assisted firing techniques such as laser-enhanced contact optimisation (LECO) that combine conventional co-firing at relatively low temperatures with a subsequent laser treatment have emerged as an appealing alternative to standard one-step cofiring.”
Improving power conversion efficiency
While TOPCon solar cells are proliferating at pace across the global solar market, they can suffer from poorer reliability compared to the more established passivated emitter and rear contact (PERC) solar cells, a problem which necessitates using a high-cost bill of materials (BOM).
In June, PV Tech Premium wrote about defects in next-generation solar modules causing significant drops in efficiency in just a few years. The major cause of this degradation in TOPCon technology was the use of the silver and aluminium mixture in the screen-printing paste because it makes the paste sensitive to corrosion.
The main driver for the use of laser-assisted firing is to gain higher power conversion efficiencies, which can range from 0.3% to 0.6% in TOPCon cells.
Laser-assisted firing, in addition, enables cell manufacturers to reduce their dependence on aluminium for forming contacts. It can either significantly decrease the amount of aluminium required in the front paste or it can even eliminate its use entirely.
Furthermore, TOPCon does not suffer from the optical losses on the front that heterojunction (HJT) technology suffers from, so Hoex is confident that the efficiency gap between TOPCon and HJT can be further reduced, particularly now that this “game changer” laser-assisted firing method has become available. He also points to an optimistic trajectory for TOPCon by describing manufacturer research and development (R&D) pipelines for the technology as “quite remarkable”.
Two stagnant decades of contact firing
The industry started to use contact firing when silicon nitride was introduced, however Hoex says solar cell contact firing methods have been “quite static” since the 2000s.
Excluding HJT technology, and some back-contact solar cells, most modern silicon PV cells have screen printed contacts that are printed on dielectric films, which act as a non-conductive, anti-reflection coating as well as a surface passivation film and hydrogenation film.
The contact firing step was predominantly needed to make contacts through these dielectric films.
Manufacturing solar cells is easiest when applying the dielectric film first as the passivation/antireflection layer, and only then performing the metallisation where the metal has to contact the phosphorous diffused emitter below the dielectric layer. In many cases the metallisation has to be aligned to a so-called selective emitter pattern that is formed in one of the previous steps.
In this case, the metallisation contains components that can “eat through” the dielectric films in order to have contact with silicon, says Hoex.
In this lies the problem, in that the emitters in the screen-printing paste must extrude through the silicon nitride layer, whilst also obtaining both a good adhesion and electrical contact with the phosphorous diffused emitter layer underneath without shunting the solar cell.
In other words, for the contact to be made through the sturdy dielectric film, it has to go through the dielectrics “quite aggressively”, but simultaneously it needs to stop once it reaches the silicon layer in order to form a good contact without going through the shallow diffused region, which would shunt the solar cell.
“That’s quite a delicate process,” adds Hoex.
This requires a co-firing step—the last process before a cell is finished—where the front and the rear contacts are fired in one step simultaneously with a high temperature of 700-800 degrees Celsius. This step is where much industry innovation has been focused on improving the paste chemistry to ensure a good contact between the layers.
This co-firing step has always been maintained as one single step using one tool with a heating zone and a cooling zone to both heat and cool down the wafers, with very relatively little innovation over the last ten years until the arrival of laser-assisted firing.
Laser-assisted firing introduction
The new process is at odds with most manufacturing innovations in that rather than reducing the number of steps in the production process, it splits one step into two steps.
In this case, the firing process is performed “imperfectly” at lower temperatures, explains Hoex. It results in only small fractions of the metal paste being in contact with the underlying silicon, while the remainder still has a partial dielectric layer in between the contact and the silicon.
This is beneficial as the areas with direct contact between metal and silicon suffer from very high surface recombination losses and areas that have an effective surface/interface passivation layer have very low surface recombination losses. This explains why these imperfectly fired cells actually have higher open-circuit voltages compared to their optimally fired counterparts.
This benefit is comparable to the significant boost that was achieved when the industry went from the aluminium back surface field (Al-BSF) solar cell to the PERC solar cell.
The Al-BSF had a full area metal contact at the rear and the PERC solar cell changed that to a dielectrically passivated rear with local contacts, where less than 5% of the silicon is in direct contact with metal. This resulted in a significant reduction in recombination at the rear and consequently increased the open-circuit voltage of the cell.
Laser-assisted firing enables a significant reduction in the metal-silicon contact fraction under the screen-printed regions, which are already less than 5% of the solar cell, with the other 95% passivated by a dielectric film. at a microscopic scale. This results in a further reduction of surface/interface recombination and thus increases the open-circuit voltage.
Solving contact resistance
The main challenge with reducing the metal-silicon contact area is the increase in resistive losses. Resistive losses scale with the resistance and the square of the current, although for clarity, this article only considers the resistive losses resulting from the silicon-metal contact.
The resistance scales with the contact resistance and inversely with the contact area, i.e., the larger the contact area, the lower the resistance. Laser-assisted firing, which is applied after a conventional firing step, focusses on significantly reducing the contact resistance at the microscopic, localised contacts.
In the laser-assisted firing process the imperfectly fired solar cell is put under reverse bias and subsequently locally illuminated by a laser. This laser light generates electron-hole pairs that are very quickly separated by the strong electric field in the solar cell resulting from the reverse bias and this results in a photo-generated current running through an external circuit.
This high current can only flow to the microscopic, localised areas, where there is direct contact between silicon and the metallisation. These areas still have a high contact resistance and experience a high current resulting in a high and very localised heating.
The laser-assisted firing process is optimised such that this local heating results in a significant reduction of the contact resistance between silicon and the metallisation, while not affecting the non-contacted areas that remain well passivated by the dielectric film.
“That’s why this two-step process allows you to get basically a screen-printed contact where part of the passivation film is still there,” adds Hoex.
Initially, scientists developed this method to recover cells that had poor contact, which they called “under firing” cells. Laser-assisted firing could fix that by improving the ohmic properties of the contact fracture.
Innovators investigating the method further exploited under-firing in order to maintain surface passivation, and then boost the contact fracture to such an extent that there is an efficiency gain.
In a previous interview, Hoex noted that UNSW had identified some concerns with the laser-assisted firing approach, and he is still unable to share specific details. UNSW scientists are seeing “interesting behaviours,” where the performance can degrade when subjected to certain treatments, but then rise again.
There can also be sensitivity to certain contaminants. It is unknown if this could happen in the field, since some UNSW cell-level tests are “quite extreme” for the sake of speed. Ultimately, Hoex says the technology is very new so there are still some questions pending.
LECO is one form of laser-assisted firing invented by German firm Cell Engineering that can improve the efficiency of PERC and TOPCon cells. Korean firm Qcells took hold of the intellectual property rights for LECO by acquiring Cell Engineering last year. A Hanwha spokesperson told PV Tech Premium that the company was not able to offer comment about the technology at this time.
Given the acquisition, it is worth noting that there has been a recent spate of patent investigations and litigations in PV technology involving the likes of JA Solar, Maxeon, Aiko, Qcells and, most recently, First Solar, with many of the incidences related to TOPCon technology.