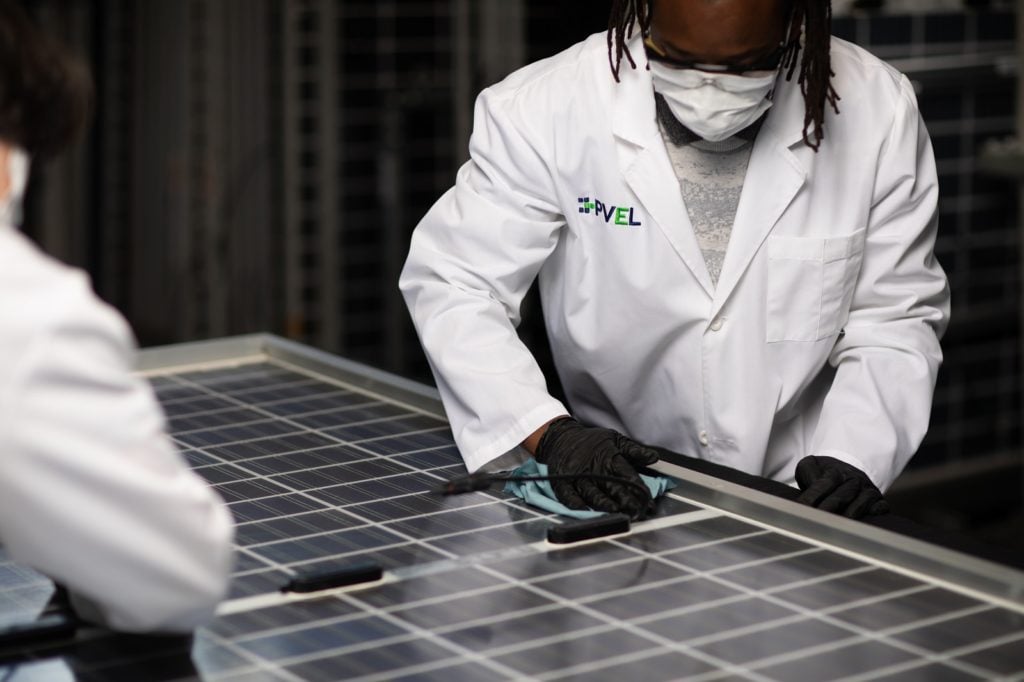
This year’s Module Reliability Scorecard from PV Evolution Labs hailed some of the solar industry’s “best ever results” in certain testing categories, but warned of increasing failure rates and mechanical stress testing concerns.
PV Tech caught up with Tristan Erion-Lorico, VP of sales and marketing at PVEL, to discuss the emerging trends and themes from this year’s scorecard, the impact of BOMs on module performance, what manufacturers must take into account during supply chain constraints and what the dominance of gallium doping means for LID.
Unlock unlimited access for 12 whole months of distinctive global analysis
Photovoltaics International is now included.
- Regular insight and analysis of the industry’s biggest developments
- In-depth interviews with the industry’s leading figures
- Unlimited digital access to the PV Tech Power journal catalogue
- Unlimited digital access to the Photovoltaics International journal catalogue
- Access to more than 1,000 technical papers
- Discounts on Solar Media’s portfolio of events, in-person and virtual
Or continue reading this article for free
PV Tech: In relation to the damp heat testing, this year’s scorecard results highlight the scale of impact that even small changes to the bill of materials (BOMs) has on module performance or reliability, could you expand on that?
Tristan Erion-Lorico: Small is obviously a relative term, some people might think changing the encapsulant, for example, would be a big change, while others might think that that would be a small change, or I think for the uninitiated, even changing the cells might be considered a small change.
We certainly see that in the same model type with different cells, we see higher amounts of susceptibility to corrosion. And similarly, changing encapsulant can also result in very different damp heat results.
I think we’ve also seen a pretty significant trend across manufacturers that glass-glass BOMs have relatively stronger performance for damp heat testing. I think in the past, there were lots of issues with the encapsulant used in glass-glass modules, and there was delamination of glass-glass modules and corrosion and other issues because the encapsulant was poor. In our testing, we see that the industry – or at least in the modules that we test – has overcome lots of those issues by using more advanced encapsulants. Now we see that there’s very few issues with glass-glass modules in our damp heat test.
But on the other side of things, with glass-backsheet modules in damp heat, that backsheet is somewhat porous and breathable and allows that high humidity to pass through the backsheet. Eventually, that humidity reaches the cells, and we’ve seen that cells can be more susceptible to corrosion than what we’ve seen in the past. We’ve observed this on a handful of different manufacturers that submit monofacial glass-backsheet modules to us.
Given the impact of those ‘small’ changes then, and against the backdrop of supply chain constraints, is it a concern that the volatility of the last 18 months, shortage of certain components or new suppliers having to be qualified, that this could have a broader impact on reliability or performance?
I think there are definite concerns. I think manufacturers that sign up for multiple BOMs for the same product type so they can have a diversified supply chain – we give kudos to those manufacturers. If customers want to procure a top-performing bill of materials or a top performing module based on PVEL’s results, and they can swap out the encapsulant or change the glass supplier if there’s supply change issues… it’s much easier on the manufacturer if there is a list of three or four or five BOM combinations. If there’s one, customers can find that quite restrictive.
The scorecard also mentions some significant failures in mechanical stress testing, but not in larger-format modules as some may have expected. What’s considered to be causing failures in mechanical stress now?
What we’ve seen is that glass-glass modules in general are more sensitive to mounting. You have to use certain clamps, and maybe you have to run the rails instead of perpendicular to the module along the frame, you have to run them in parallel.
Following the manufacturer’s mounting methods is much more critical for glass-glass modules than glass-backsheet. Once you do follow those mounting methods, glass-glass modules perform extremely well in the mechanical stress test, but if you take those mounting instructions for granted, some of them can be quite limiting [and] you might break the glass, rear or front, or have the glass pop out of the frame.
I think the finding is probably that mounting instructions in the manuals, which probably a lot of people don’t follow, are critical for glass-glass modules.
But just because large-format modules that we test and see good results from, that doesn’t give large-format modules a free pass across the board. I think that the manufacturers we’ve tested large-format modules for have done their due diligence on frame design, encapsulant etcetera, and there’s probably others that haven’t done such a good job, but we haven’t seen them in PQP testing.
Gallium doping seems to be ever present in modules released today, which is seemingly impact on incidents of specific degradation?
We’re seeing the vast majority of mono PERC modules that we test use gallium doping, to the point where I recently had a company submit their BOM with boron and I asked if it was a typo. We see gallium pretty much across the board and that has certainly resulted in record low LID values. It’s to the point where I question a little bit why manufacturers with very little LID are still producing relatively high year one degradation rates on their data sheets and warranties.
Historically that 2.5% or 3% first year degradation was attributed to LID, right? Now we’re measuring 0% or very close to zero on a lot of modules, but the data sheets still say 2, maybe 2.5 or 3% year one degradation.
Comparing mono PERC to other module types, are there any early trends you’ve identified from n-type, specifically TOPCon modules that have been tested?
Unfortunately we haven’t tested enough TOPCon modules to really look at trends. Typically what’s submitted for testing is about a year after product announcements, so we’re talking to manufacturers now about TOPCon modules released at SNEC [2021]. For some of the initial or early adopters of TOPCon, we’ve seen quite a large range in the results. Some of them are very good, some of them it looks like they need to address some fundamental issues in the cell design. But we haven’t seen enough to really know if there are trends compared to mono PERC results.