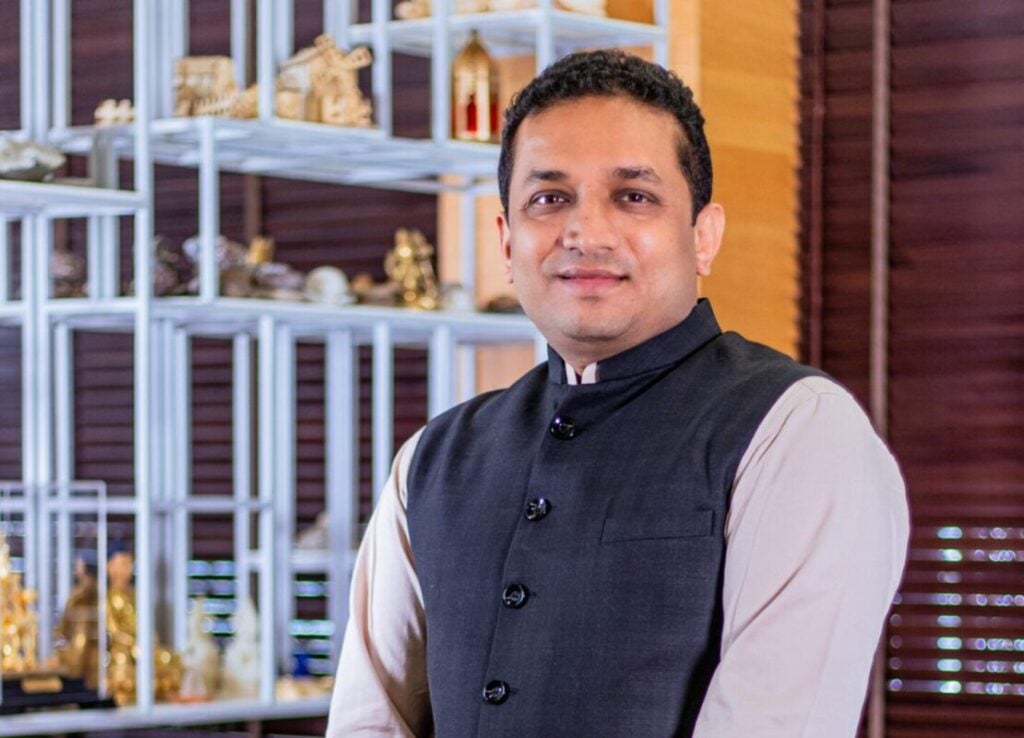
Off the back of announcing India’s first ever AI-powered solar manufacturing line, the founder of Indian solar manufacturer Goldi Solar tells PV Tech Premium that plans to scale up operations from 3GW to 14GW by mid-FY26 would not have been possible without using AI.
Earlier this month, Goldi Solar launched its pioneering AI-driven factory in Surat, Gujarat, with plans to scale to an enormous 14GW of production capacity in a short space of time, thanks to a vast list of technical optimisations and enhancements via AI.
Unlock unlimited access for 12 whole months of distinctive global analysis
Photovoltaics International is now included.
- Regular insight and analysis of the industry’s biggest developments
- In-depth interviews with the industry’s leading figures
- Unlimited digital access to the PV Tech Power journal catalogue
- Unlimited digital access to the Photovoltaics International journal catalogue
- Access to more than 1,000 technical papers
- Discounts on Solar Media’s portfolio of events, in-person and virtual
Or continue reading this article for free
“AI plays a crucial role in optimising inspection processes, ensuring accuracy and minimising errors—key factors for rapid scaling,” says Ishver Dholakiya, founder and MD of Goldi Solar. “Without AI, maintaining high manufacturing efficiency at this level would be significantly more challenging.”
Thoroughly testing AI
The AI technology integrated into Goldi Solar’s operations has been sourced from international partners, says Dholakiya. It went through a comprehensive evaluation by the company’s in-house research and development (R&D) team at its manufacturing facility, including rigorous testing to ensure its reliability, efficiency and seamless integration.
This required the engineering team to conduct extensive on-site evaluations overseas for several months, verifying machine output and cycle times. The engineers also carried out rigorous Factory Acceptance Testing (FAT) on each machine before deployment to ensure optimal performance.
“Additionally, we are upgrading our existing machinery with AI-driven capabilities to further enhance efficiency and precision,” notes Dholakiya, in what could hardly be a greater sign of the company’s approval of the new AI technology.
AI versus conventional manufacturing
Differences to conventional, non-AI-driven manufacturing are stark. Indeed one of the most eye-catching statistics from the original factory launch news was that the pioneering technology includes automated high-speed stringers that can achieve a production capacity of 10,000 cells per hour.
Dholakiya claims that in conventional manufacturing defect rates typically range between 8-10%, leading to material wastage and production inefficiencies. Whereas, by integrating AI, Goldi Solar has successfully reduced defect ratios to below 2%, ensuring higher precision, consistent quality and minimal rework.
AI-driven inspection systems allow for real-time defect detection, preventing faulty cells from progressing further in the production line. Meanwhile, AI-powered predictive maintenance helps prevent unplanned downtimes, further improving operational efficiency and ensuring maximum throughput at optimal speed.
“This results in greater yield, cost savings and enhanced overall productivity, setting a new benchmark in solar cell manufacturing,” says Dholakiya.
Through the use of AI, cycle times have improved by 70%, resulting in this significant boost in production efficiency. Dholakiya also notes that while AI technology does require a higher initial investment, he is confident that its use can reduce material wastage and eliminate errors, ultimately leading to substantial cost savings and enhanced overall productivity.
Adapting to challenges
The company is currently manufacturing both passivated emitter and rear cell (PERC) and tunnel oxide passivated contact (TOPCon) technologies, but with a major focus on TOPCon. However, its existing machinery is adaptable and can be upgraded to produce heterojunction (HJT) technology.
“Looking ahead, based on market demand, we plan to expand our portfolio to include HJT modules,” Dholakiya forecasts.
A key global concern about AI is the potential effects on job creation. Asked for comment on this, Dholakiya says that AI primarily enhances inspection processes, improving efficiency and accuracy, but the expansion to 14GW has significantly increased manpower requirements across various functions.
“AI has complemented rather than reduced job creation,” he claims. “To date, we have created employment opportunities for 7,000 individuals. We are also committed to empowering local communities, including tribal populations and promoting women’s empowerment. One of our production lines is exclusively managed by women, reinforcing our dedication to inclusive growth and workforce diversity.”
Earlier this month, India’s Ministry of New and Renewable Energy (MNRE) also stated that imported wafers would not qualify for classification as ‘domestically produced’. The government has sought to to incentivise domestic production of solar products, but the effects this might have on Indian solar cell producers have yet to be clarified.
However, modules from the factory are not entirely bound by India’s domestic content focus, with Dholakiya confirming a commitment to serving both domestic and international markets.